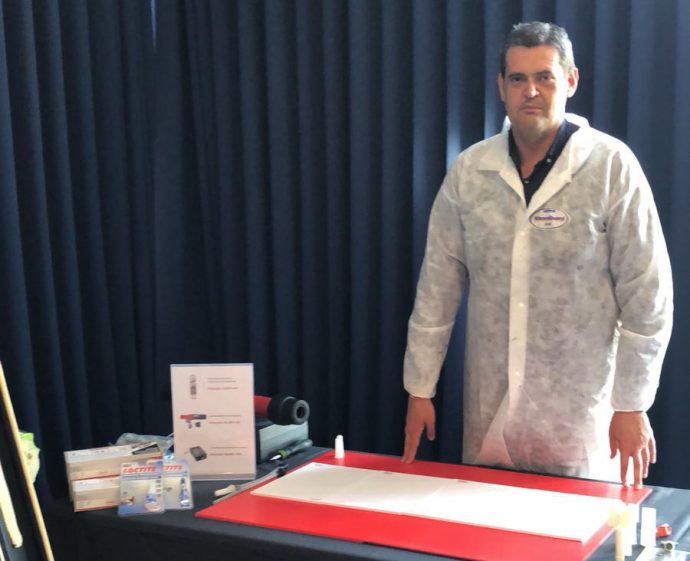
Henkel es un transatlántico industrial que aporta soluciones en distintas áreas de negocio. ¿Cómo os reconocen los profesionales de la reparación y el mantenimiento de vehículos en España? ¿Bajo qué marcas o gamas de producto llegáis a los talleres?
Para las aplicaciones de fijación, sellado, montaje y protección de componentes mecánicos, es decir, para todo tipo de químicos que precisan los profesionales de los talleres mecánicos, trabajamos con la marca LOCTITE, que es en el ámbito de España y Portugal la más conocida en este sector. Disponemos, además, de la marca TEROSON para trabajos de montaje y reparación en taller de carrocería. Por último, llevamos unos años introduciendo con éxito la marca BONDERITE, que incorporamos en reparación del automóvil para la limpieza integral de piezas mecánicas y de carrocería.
En un mercado en constante evolución como es el del automóvil, ¿cómo se adapta la compañía a esta realidad? ¿Cuáles han sido los últimos productos que habéis lanzado?
Nuestra vinculación a los avances tecnológicos en la fabricación de los vehículos y la creciente innovación tecnológica que se está generando en el Primer Equipo, en donde somos socios tecnológicos clave de las principales compañías automovilísticas, nos permite ofrecer de forma continua nuevos productos bajo las premisas básicas de ahorro de costes y simplificación de los procesos de trabajo, ofreciendo soluciones con mejor comportamiento en seguridad e higiene para los trabajadores.
Bajo estas premisas, algunos de nuestros últimos lanzamientos han sido los adhesivos híbridos, con una tecnología exclusiva y patentada por Henkel y que son capaces de adherir de forma mucho más fiable los nuevos materiales y diseños de piezas que se están generando en los vehículos; los adhesivos de lunas parabrisas de última generación, con Certificación HMLC y que permiten adherir todo tipo de lunas en carrocerías de acero y aluminio con un tiempo de inmovilización de únicamente 30 minutos; y nuestra masilla epoxi bicomponente de última generación, ideal para sustituir el proceso de estañado y que ni precisa de la aportación de calor (que distorsione la chapa y que por lo tanto no requiere del desmontaje de la pieza) ni genera humos tóxicos o peligrosos.
Los lectores interesados en conocer todos nuestros productos y novedades con mayor detalle, pueden hacerlo a través de la página web www.reparacion-vehiculos.es y del blog para profesionales RUTA 401.
¿Es consciente el profesional de las ventajas que supone trabajar con vuestros sistemas?
Afortunadamente, el sector reparador confía y apuesta cada vez más por las soluciones adhesivas, que pueden complementar e incluso sustituir los procesos tradicionales de soldadura, atornillado y remachado para el montaje en carrocería. De hecho, son los profesionales quienes nos piden cada vez más productos con mejores prestaciones en seguridad e higiene.
Existen evidentes ventajas en la unión adhesiva de las piezas, como sus propiedades anticorrosivas y de aislamiento acústico (montaje y sellado en una única operación) o la reducción de los tiempos de trabajo en la preparación previa de los puntos de soldadura, orificios para el remachado, su posterior afinado y conformado, etc. Además, este tipo de unión no precisa de la exposición de las piezas a temperaturas elevadas, permitiendo un ahorro de energía y evitando la distorsión y debilitamiento térmico de las piezas, logrando en definitiva una unión más robusta.

Reparación de un techo con TEROSON EP 5065
¿Y qué respuesta lográis dar en cuanto a tendencias adhesivas para satisfacer esa demanda?
En la unión adhesiva, actualmente trabajamos en tres vías: los epoxis estructurales bicomponentes, los adhesivos en base a polímeros MS de alto módulo y los poliuretanos bicomponentes «Grado ME».
Los primeros son adhesivos de prestaciones idénticas a los de Primer Equipo que adhieren y sellan con alto nivel de resistencia paneles metálicos y de fibra con buena coincidencia entre los mismos. Aunque es bicomponente, se presenta en un cómodo cartucho de plástico fácil de extruir y que reduce la generación de residuos por envases vacíos del taller. Un ejemplo de estos epoxies es TEROSON EP 5065.
Los polímeros MS, como TEROSON MS 9220, ofrecen un excelente comportamiento en seguridad e higiene y sirven para adherir planchas metálicas, de fibra o plástico, incluso en vertical o en uniones no coincidentes gracias a su capacidad de relleno y resistencia al descolgamiento.
Finalmente, los poliuretanos «Grado ME» tienen un nivel de emisión por debajo del umbral de ingredientes potencialmente peligrosos o cancerígenos, como el isocianato, y también ofrecen un fantástico comportamiento en seguridad e higiene. TEROSON PU 6700 ME es uno de nuestros productos principales en esta categoría.
En términos de seguridad, ¿existen avances relevantes en el terreno de la adhesión?
La seguridad, en términos de salud e higiene y en simplificación de los procesos de reparación, es una meta prioritaria para Henkel. En las anteriores respuestas hemos mencionado nuestras líneas de actuación en innovaciones y unión adhesivas que, junto con nuestra línea de productos de limpieza BONDERITE, inciden en factores muy a tener en cuenta.
Hablamos, en el caso de las tres vías mencionadas en la anterior respuesta, de productos más benignos de uso para el trabajador y con mejor comportamiento. También de productos y procesos más simples, minimizando el riesgo durante el trabajo (menos etapas y más sencillas) o exentos de la generación de humos o altas temperaturas (toxicidad, riesgo de quemaduras, etc.) con nuestros epoxies TEROSON EP 5065 y TEROSON EP 5010 TR.
Adicionalmente, nuestros productos de limpieza concentrados en base agua y biodegradables, como la línea BONDERITE, suponen una gran mejora medioambiental en la depuración y tratamiento de los efluentes y residuos líquidos que genera el taller. Todo ello, siendo por supuesto más seguros que los habituales desengrasantes y disolventes en base solvente.
¿Existen procesos en la reparación de vehículos en los que algunas técnicas tradicionales ya no se usen o estén directamente prohibidas?
Sí, en efecto, ya lo hemos mencionado al explicar nuestra masilla sustituta a los procesos de estañado TEROSON EP 5010TR. Con este material se realiza un conformado superficial de mayor nivel de adhesión y calidad superficial en las zonas enmasilladas y reparadas que la ya prohibida aportación de aleaciones de estaño y plomo que hasta ahora se realizaba. Y es que el proceso de estañado, aparte del peligro inherente de quemaduras, genera humos tóxicos o potencialmente cancerígenos que no tienen lugar trabajando con nuestros productos.
Otra vía de trabajo, no prohibida pero tremendamente costosa y que poco a poco debe ir entrando en desuso, es el empleo de la soldadura en la unión de planchas como techos y paneles laterales. Gracias a adhesivos estructurales como TEROSON EP 5065, estos procedimientos de unión no solo son más seguros sino también económicos, al no precisar de máquinas complejas ni de la aportación de calor.
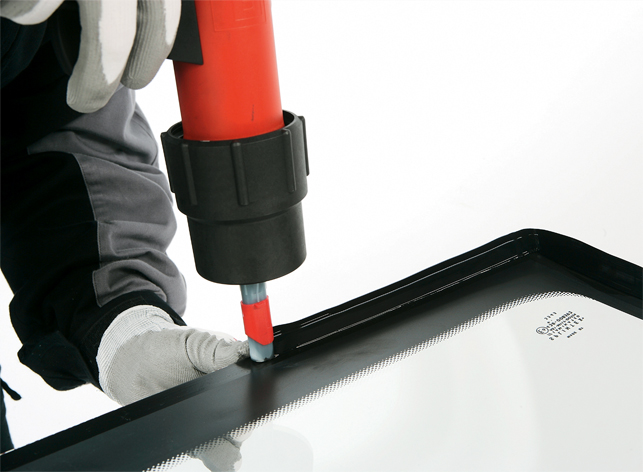
Adhesivo TEROSON PU 8597 HMLC para el pegado de lunas
Una de vuestras especialidades es, sin duda, los productos para el pegado de lunas parabrisas. ¿Cómo podéis ayudar a vuestros clientes en estas reparaciones tan poco usuales y que a menudo implican una dificultad añadida?
A nivel de sustitución de lunas pegadas, la ayuda que prestamos a los talleres va en dos vertientes. Por un lado, la fiabilidad y simplicidad en nuestra gama de productos ante los nuevos diseños de carrocería y tipos de lunas parabrisas. Con el uso de adhesivos con Certificación HMLC, como pueden ser TEROSON PU 8730 HMLC o TEROSON PU 8597 HMLC, el taller tiene la certeza que está aplicando el adhesivo adecuado, sea cual sea el peso y tamaño de la luna, su posición de montaje respecto al marco de la carrocería o los dispositivos electrónicos que lleve adosados y/o serigrafiados.
Por el otro, el siempre a tener en cuenta ahorro de costes: No solo suministramos productos fiables sino procesos que minimizan el gasto en producto (con el uso de nuestra exclusiva boquilla deslizante) y acortan los tiempos de inmovilización para una mayor rotación (y facturación) de vehículos en el taller. En este sentido, cabe destacar TEROSON PU 8730 HMLC que, testado bajo los últimos y más exigentes tests de impacto real que existen, posibilita mover el turismo con la luna pegada en apenas media hora.
A la vista de toda esta información, queda clara vuestra condición de empresa de Base Tecnológica. ¿Qué garantías supone para los mecánicos trabajar con vuestros productos?
La principal razón por la que un profesional de reparación de automoción puede confiar en nuestros productos y sistemas de reparación es la misma por la que en el Primer Equipo merecemos la confianza de las principales marcas del sector: nuestra profunda experiencia en el montaje y fabricación de todo tipo de vehículos. En el ámbito de la fijación y sellado mecánico, todas las compañías automovilísticas emplean en los puntos críticos del motor y componentes mecánicos productos y tecnología LOCTITE para el montaje de sus componentes. Productos y soluciones que han sido consensuados en la fase de diseño junto con los ingenieros de estas empresas. Y lo mismo ocurre con nuestra marca TEROSON en el montaje y protección de las carrocerías en las fábricas de coches.
Pues bien, esta misma experiencia en el Primer Equipo se traslada de forma precisa a los procedimientos avalados por estas compañías en el Recambio Oficial. Por ello, el profesional reparador tiene la certeza que a la hora de reparar el vehículo con nuestros productos obtendrá el mismo nivel de fiabilidad que el de los vehículos fabricados en todas las cadenas de montaje.
¿Y para los que el taller es su negocio? ¿Qué diferencias deben entender los empresarios de nuestro sector que existen entre la vuestra y otras propuestas del mercado?
En el mercado de carrocería, el modelo de negocio ha cambiado mucho durante los últimos años debido a la reducción de los costes de operación, así como en los tiempos asignados para cada reparación; una realidad que nos impulsa a mejorar nuestros productos, procesos de aplicación y tiempos de secado. Por otro lado, la reproducción de acabados de fábrica supone una ventaja competitiva para cualquier taller ya que permite marcar una diferencia en la calidad del acabado final de sus trabajos. También la reducción de los tiempos de secado en adhesivos nos permite mejorar la rentabilidad de los talleres y marcar una diferencia respecto a nuestros competidores.
Más información en reparación-vehículos.es
No hay comentarios
Escribir comentarioLo siento, debes estar conectado para publicar un comentario.
Artículos relacionados